Jake Pointer is a first year Sociology PhD student studying the lives of workers in the meat processing industry. Here he shares some thoughts on his recent trip to a chicken processing plant in County Durham.
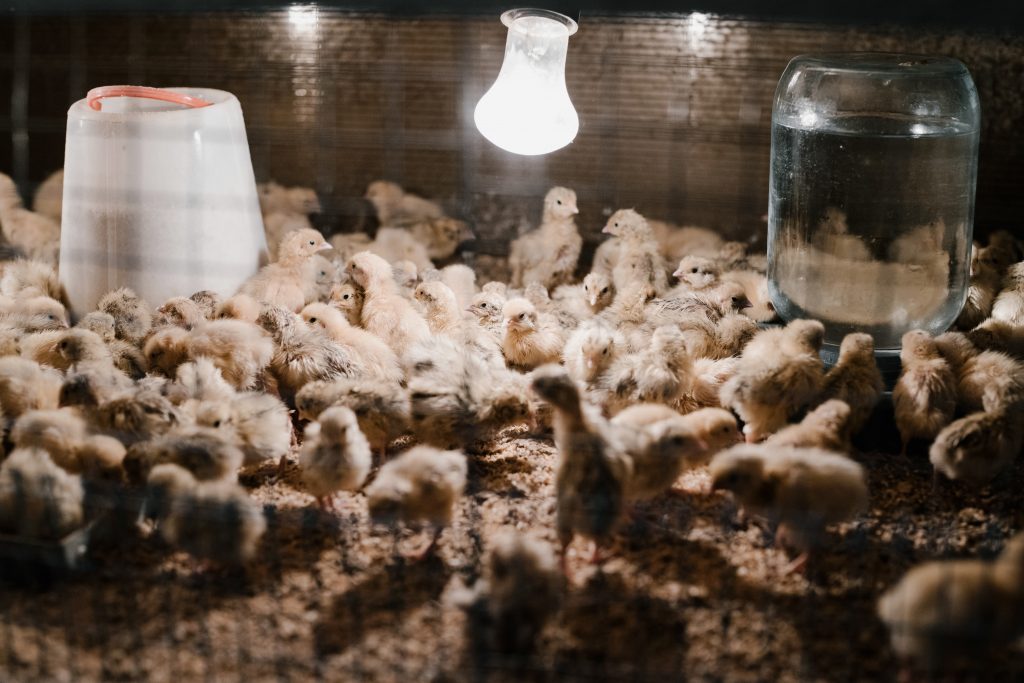
In late February, I had the chance to visit a chicken processing plant in County Durham on a university trip organised by the Centre for Rural Economy. As my research concerns those working in the meat sector, it was an excellent chance to have my first glance into the working lives within such a facility. I went into this with mixed feelings: my vegan beliefs are naturally against any meat-orientated food producers, but my scholarly mind was telling me to put my biases aside and go in as objectively as possible. In this context, and as I’m quickly learning is the case for all my research, the scholarly mind was certainly the appropriate one to tap into for this visit (although this is sometimes challenging).
On arrival to the plant, the first thing I noticed was the smell of (perhaps not surprisingly) chicken. As we walked through the large gates and into the reception the smell only grew stronger until, for me at least, it was almost overpowering. After a brief talk from one of the managers about the plant we were split into groups and were given a tour. Before entering the processing areas we had to gear up with protective clothing and hairnets as well as wash our hands thoroughly. It seemed to me health and safety was of high importance here.
Inside the working areas were large machines, which, in various ways, processed the chicken. Slicing, freezing, cooking, bagging, skinning; there was a machine for everything. Many of the workers engaged in these machines had seemingly monotonous tasks, often involving repetitive motions such as continuously unloading a box of chicken pieces into a machine. Within the arrival area it was very cold as this is also where the chicken carcasses enter the plant and so they need to be kept fresh before being processed. This also means that plenty of workers operate in a cold environment. It was also quite loud in the factory, with various machines working away as well as speakers playing music here and there. Having worked in a warehouse some years ago myself, I can appreciate the effect music has on making an otherwise monotonous and often boring task more tolerable.
Whilst the tour was focused on the chicken, I was almost always looking at the workers, trying to use my sociological imagination and see if I could notice anything of interest. Some of the safety signs I noticed were in Polish next to their English counterparts, an indicator of the presence of non-British workers. I felt translating these signs was good work practice as safety should, in my opinion, be the priority in a potentially dangerous job such as this. The work-ethic seemed very high, with the workers seemingly never stopping whatever they were occupied with for even a second. I would not say they looked happy, but rather indifferent to their tasks, almost robotic as ever more chicken came through ready to be loaded into this machine or that. Few were talking at all, with most applying their attention only to their task. I would say that all the jobs required focus as the machines operated at high speed and a lapse of concentration would hinder this, and as a result, production. Many of the jobs also looked very physically demanding, often involving the lifting of large boxes or pulling huge pallets stuffed with chickens.
After the tour, we were led to the small conference room for a short Q and A session with the director of the company. The majority of questions were about the chicken itself; the quality, the manufacturers supplied and so on which the director and his mangers were happy to answer. It was clear they were proud of their work there, supplying high-quality, British ‘protein products’. I inquired about the workforce, in relation to the Polish signs I saw, and was told that around 30% of the employees were Polish. In addition, I was interested to see if they ever have injuries and if so, what the common ones were. The Director seemed a little surprised at my question. The Operations Manager told me the majority are made up of cuts, slips or back problems. I was surprised by how open they were about this. These answers raised more questions in my mind, why so many Polish workers? How are the injuries dealt with? but as I was there as part of a group, I did not want to dominate the session. A question was also posed about the vegan food factory which was operating just up the road. The director was very open to the changing food market and told us it was the company’s responsibility to adapt accordingly. He made a point that the businesses that do not adapt are the ones that close down.
I went away from this trip with mixed feelings. The scholarly side of me was happy with such an opportunity and experience, and I found observing the working environment fascinating. Worker safety did seem a high priority, which I was pleased to see. However, I would have been intrigued to hear from the employees themselves; their thoughts on the job, if they enjoyed working there, job prospects, what they thought of the management, whether the non-British workers integrated well and whether anyone ever thinks of the chickens at all and how they fit in with the process? These questions I will have to save for another day; with a bit of luck, my research will help answer these and other questions in the future.