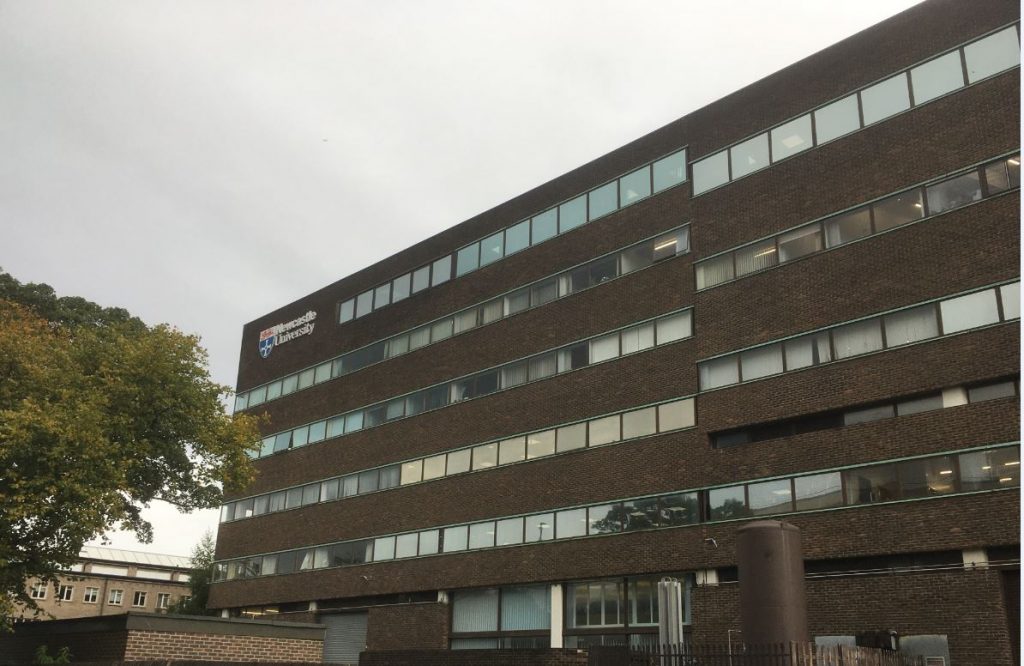
I have recently become the school of Engineering’s Deputy Director of Business and Engagement. This role covers aspects of internationalization, employability and outreach. It will allow me to continue my outreach and STEM work as well as enhancing the school’s engagement with industrial contacts.
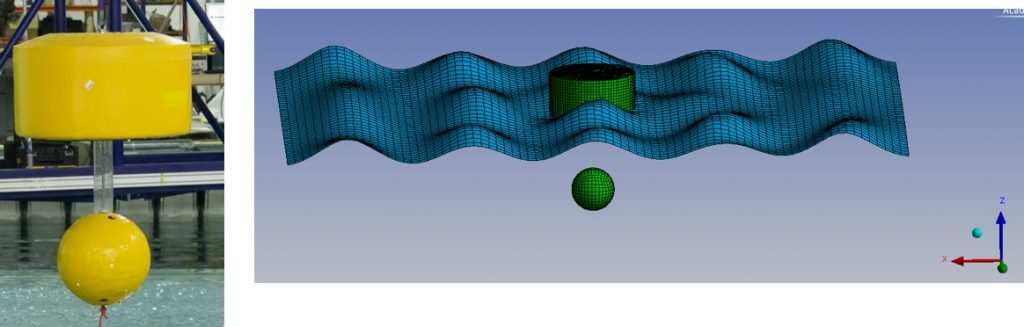
In January 2019, the electric drive developed as part of our EDRIVE project was transported to Flo-wave tank located at Edinburgh University. It was mechanically coupled to a scale model of a submerged heaving buoy – a device developed by industrial partner Carnegie. The buoy, machine and power converter were tested in a range of sea-states and control regimes in the wave tank. At full scale, it is envisaged that the submerged heaving buoy would have the power take off situated below the buoy. For testing purposes, the power take off unit was located above the water line and coupled to the buoy via a pulley system. As the buoy tested was operated fully submerged, it had no hydrodynamic stiffness and was hence not representative of a whole class of wave energy converter. In order to demonstrate the EDRIVE system applying a variable spring stiffness, a surface piercing buoy was built (with thanks to mike @ https://www.fountaindesign.co.uk ) . To manipulate the resonant frequency to a representative sea state, it was coupled to a submerged mass. The hydrodynamics of the buoy were investigated by Elie Shami, a PhD student from RMIT, Melbourne, Australia
In August 2019 a final set of testing was done at FloWave. The new buoy had a distinct heave resonant frequency which as used to demonstrate the effect to of varying spring stiffness on the oscillation. In addition the maximum power transfer controller was used to tune the device at a number of different sea states. The controller was developed by Luke McNabb, who was visiting us from RMIT for 3 months. You can see Luke getting fully involved in the testing.
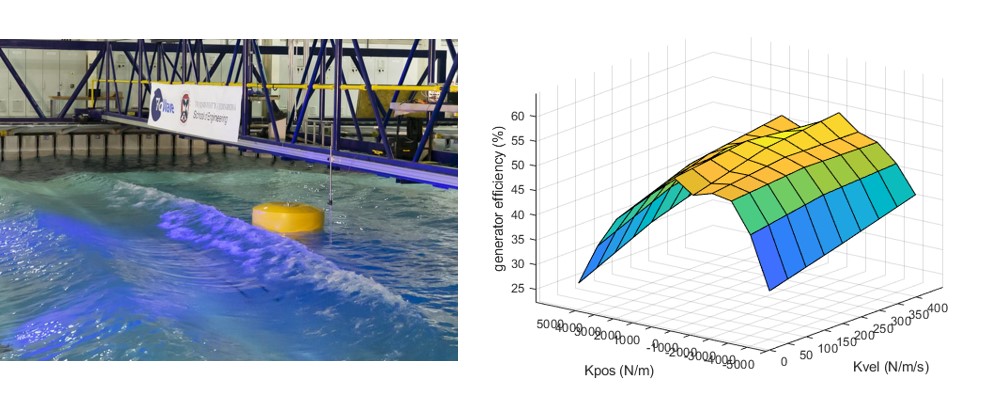
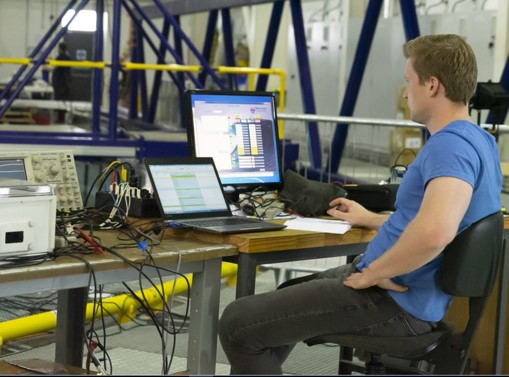
Between us, fully controlled direct electrical power take off of a scaled wave energy converter was hence demonstrated. A representative control algorithm was used to prove that electrical systems could control the oscillation, and that bidirectional power flow could be achieved in a pure electric drive train. Many thanks to Steve McDonald, Luke, Elie, Markus Mueller (Edinburgh) and Mike from fountain design (https://www.fountaindesign.co.uk) for making this project happen .
I recently discovered that ex-PhD students of mine are now working at universities in China and Iran, plus employed in the private sector in companies in Wales, England and Saudi Arabia. Reassuring that students I have worked closely with for at least 3 years are going off to do good things in the wider world.
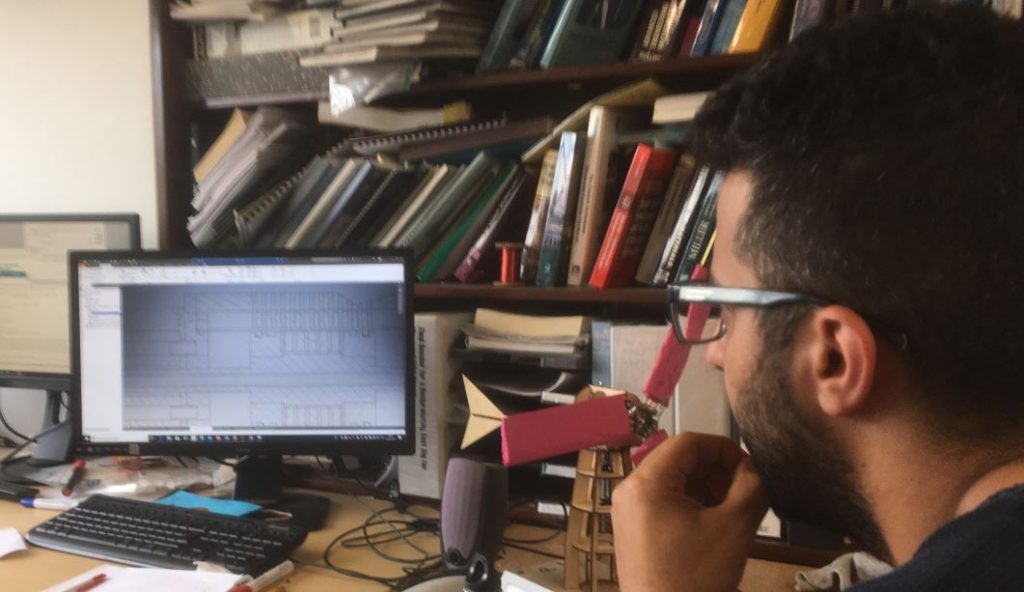
A good day at work.
Taking machines from the computer screen to the laboratory and then onto a commercial product. This month I was coordinating work on the electromagnetic design, the mechanical design, the coil winding, component pressing and assembly of a new machine across 4 partners. Here is a 3d printed mock-up of a new stator design we are hoping to make from SMC.
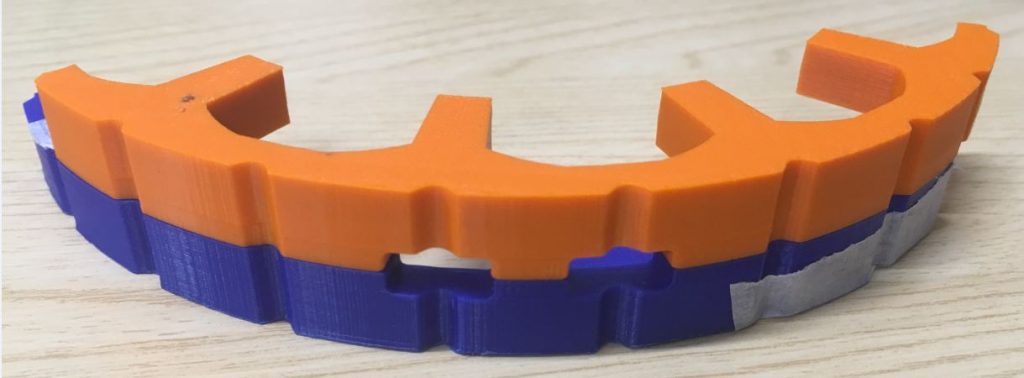
In other work, we are approaching the build phase of a new linear machine, and closing the test phase of an in wheel motor.
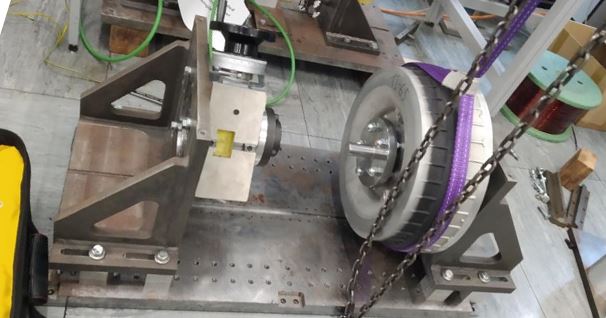
Another first for me: visiting an undergraduate field trip. As part of the re-launch of our undergraduate degrees, there are some huge improvements coming on stream September 2020, including a field trip and an iinterdisciplinary group project including an electrical drive.